Redefiniendo el Levantamiento de Inventario en la Manufactura
En el mundo de los negocios, la búsqueda constante de eficiencia y mejora es esencial para mantenerse competitivo en un entorno en constante cambio. Una empresa dedicada a la manufactura con más de 90 empleados enfrentaba un desafío que demandaba soluciones innovadoras: el proceso anual de levantamiento de inventario. Este proceso, que llevaba tres meses completar y generaba gastos significativos en horas extras, estaba a punto de someterse a una transformación radical.
El proceso convencional de levantamiento de inventario se realizaba durante 12 semanas, de 5 de la tarde a 10 de la noche, lo que requería el pago de horas extras dobles y triples. Esto no solo afectaba los costos operativos, sino que también resultaba en una falta de información actualizada, ya que el valor del inventario se obtenía tres meses después, volviéndose obsoleto para tomar decisiones estratégicas en un entorno donde los inventarios se movían constantemente.
Reingeniería para abordar el desafío
Durante los 15 años previos, se habían llevado al cabo distintas iniciativas para intentar mejorar el proceso de levantamiento de inventarios que si bien habían dado algunos resultados, los beneficios no podían ser mayores al 10% por lo que se estuvo discutiendo de qué manera sería posible desarrollar una aproximación distinta que pudiera de alguna manera proveer información respecto a las existencias y valor del inventario en un tiempo menor a las 12 semanas que actualmente tomaba
El punto de inflexión llegó cuando la empresa decidió abordar este desafío a través de un proceso de reingeniería. La reingeniería es una metodología que implica una revisión radical y el rediseño de procesos con el objetivo de lograr mejoras significativas en eficiencia, reducción de costos y creación de valor. En este caso, el enfoque estaba en el proceso de levantamiento de inventario.
El proceso de reingeniería no fue una tarea sencilla; llevó dos años en total. Durante este período, la empresa se embarcó en la identificación minuciosa de cada uno de los productos en su inventario, desde componentes de varias toneladas hasta pequeños tornillos milimétricos. Este proceso se desarrolló en paralelo a la operación normal de la empresa para no interrumpir sus actividades. Tropezones iniciales y desafíos emergentes llevaron a la creación de un área especializada para la identificación y marbeteado de productos que carecían de identificación.
Con el objetivo de agilizar el proceso y garantizar el éxito, se llevaron a cabo pruebas preliminares durante los últimos tres meses antes del levantamiento de inventario del tercer año. Se implementaron lectores de códigos de barras inalámbricos, se desarrollaron interfases y plantillas de carga de existencias para asegurar la precisión de la información.
Finalmente, llegó el día del levantamiento de inventario. La alta dirección tomó la decisión de dedicar toda una semana al proceso. El primer día, desde las 9 de la mañana hasta las 10 de la noche, se trabajó intensamente en la identificación de los productos. La colaboración de la plantilla, previamente asignada a roles específicos, fue esencial para el éxito del proceso.
Al final del primer día, el 95% de los materiales ya habían sido inventariados, y el 90% de los colaboradores había completado sus tareas, quienes a esa hora podían dejar las instalaciones de la organización para irse a sus casas con la satisfacción de haber logrado la meta establecida. Las últimas identificaciones se llevaron a cabo hasta las 7 de la noche, lo que resultó en un pago de solo 2 horas extra para un grupo reducido de personas.
La optimización no se detuvo ahí. Se ejecutaron macros de Excel para preparar las plantillas de carga de información en el sistema ERP, se realizaron pruebas y finalmente se procedió a la importación de los datos, que concluyó a las 11 de la noche.
Este proceso rediseñado permitió que, para la mañana siguiente, los directivos tuvieran información precisa sobre el costo del inventario en tiempo real. Este cambio significativo en el flujo de información tuvo un impacto directo en la toma de decisiones. Ahora, con una comprensión clara de los niveles de materia prima y productos terminados en los almacenes, la empresa pudo establecer planes de producción y comercialización más efectivos, lo que llevó a un aumento del 15% en la facturación adicional en comparación con años anteriores.
En resumen, la reingeniería se convirtió en la herramienta que permitió a la empresa superar los desafíos asociados con el levantamiento de inventario. Reducir el costo de tiempo en un 97% y lograr una toma de decisiones más informada y ágil demostró el poder de la innovación y la determinación en la búsqueda de la excelencia operativa. En la próxima parte, exploraremos los pasos específicos que llevaron a esta transformación y cómo se implementaron con éxito.
Continuará…
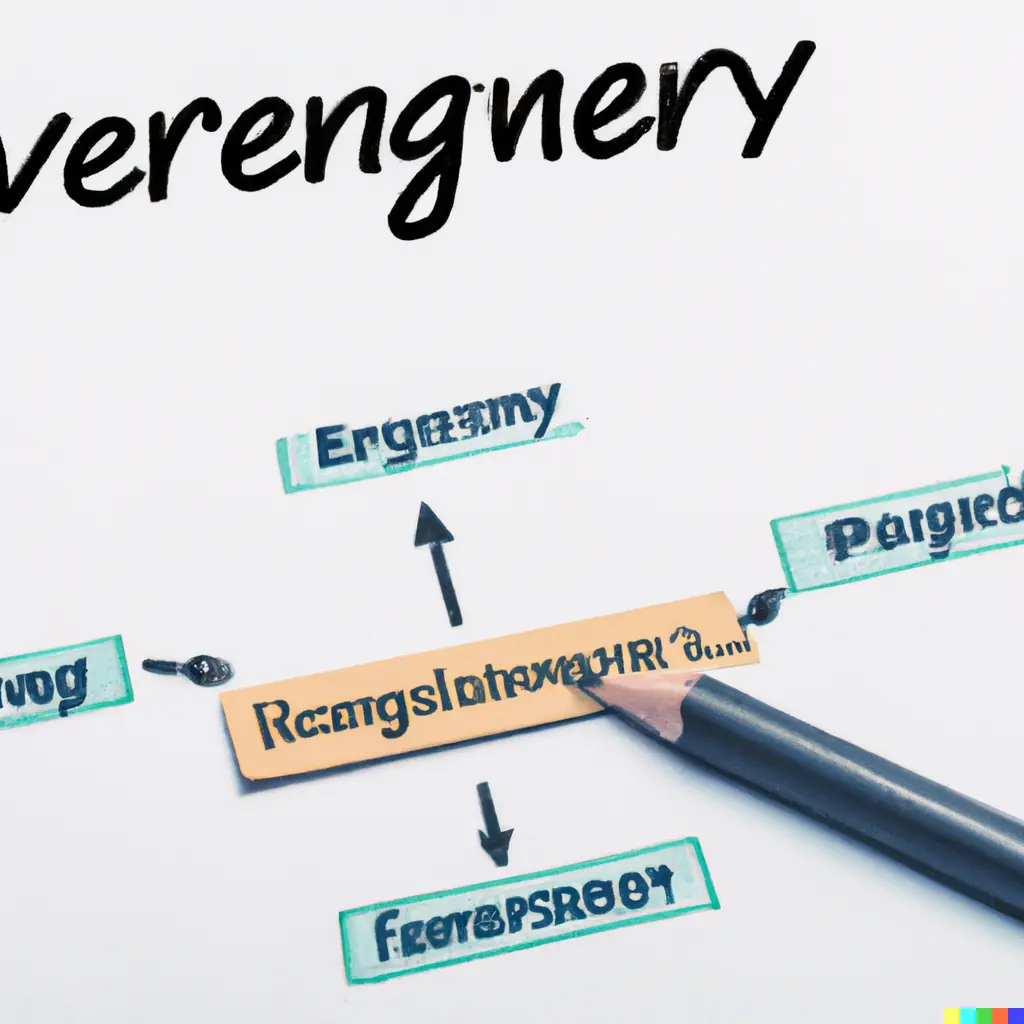